Repair for a more sustainable industry
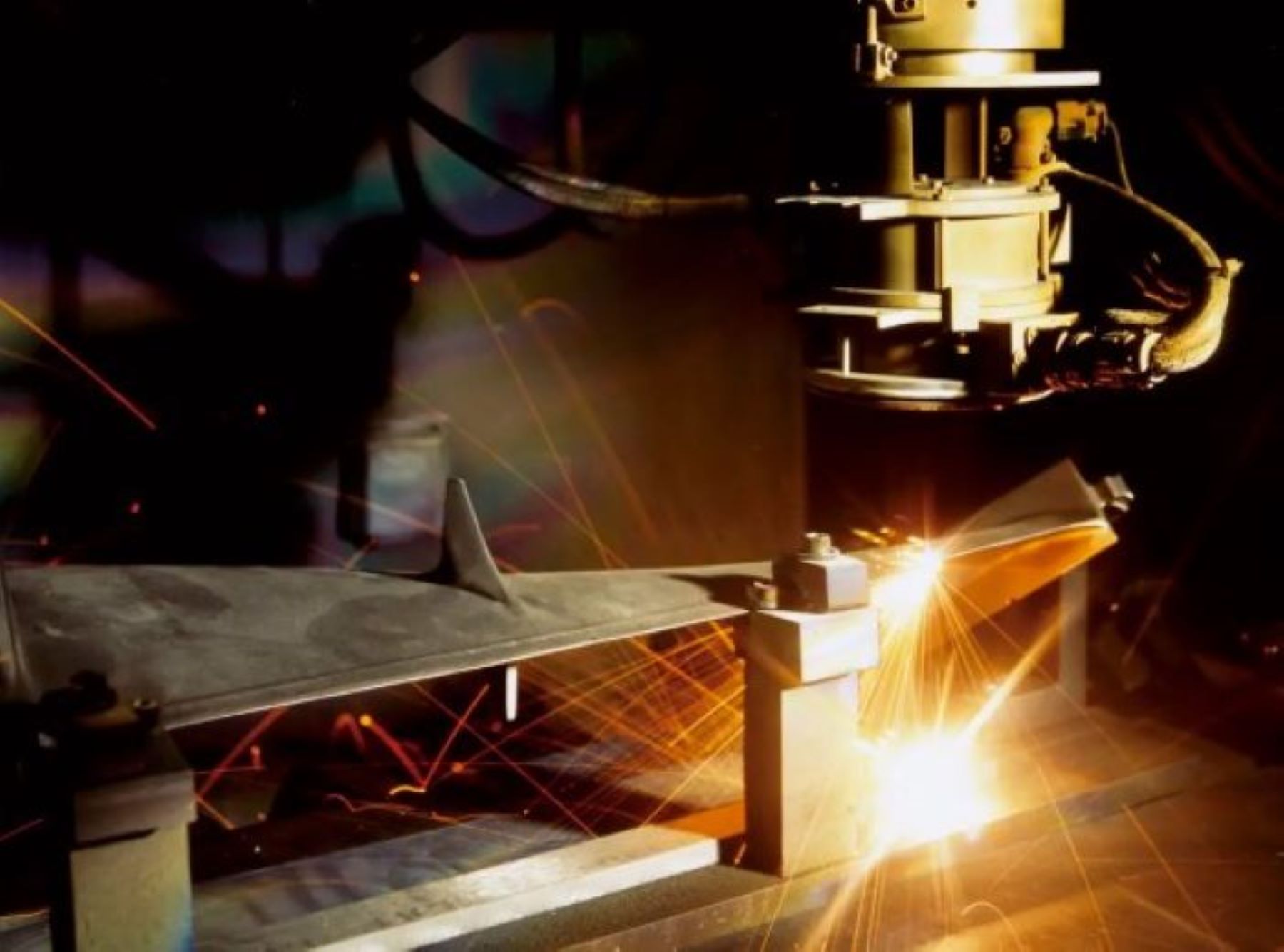
The School of Engineering at Jönköping University has secured several research projects in sectors such as aerospace, automotive and material suppliers in the area of "Circularity by Repair". Photo: GKN Aerospace Sweden
As industry strives for sustainability, the concept of "Circularity by Repair" has become increasingly important. The School of Engineering (JTH) at Jönköping University (JU) has several research projects on this theme in various industrial sectors, including the aerospace industry.
“Extending the lifetime of metal components reduces the need for remanufacturing and recycling. It thus reduces material waste, energy consumption and carbon emissions, contributing to a greener and more resilient manufacturing sector,” says Ehsan Ghassemali, Professor of Materials and Manufacturing – Casting, at the School of Engineering at Jönköping University (JU).
Recycling and remanufacturing are common strategies in the circular economy, but in many cases, repair is the most energy and resource efficient choice. It allows materials and components to be used for longer, without losing their quality.
“Together with our partners, we are leading the way towards a more efficient, responsible and forward-looking manufacturing industry. Especially when it comes to strategic components, the question is no longer whether they can be remanufactured, but how they can be repaired in a sustainable and efficient way,” says Ehsan Ghassemali.
Extending the life cycle of products
A good repair should provide the same performance in the repaired part as in the original, which poses some challenges. To address these challenges, JTH has secured several research projects in sectors such as aerospace, automotive and material suppliers. The research ranges from the development of advanced material testing techniques to AI-based tolerant alloy design and process optimization.
“These initiatives are in line with the EU Circular Economy Action Plan, which emphasizes the role of repair in extending product lifecycles and reducing waste,” says Ehsan Ghassemali.
A key strategic area
Ceena Joseph, Principal Research Engineer at GKN Aerospace Sweden, which makes engine components and cabin windows for aircraft, says repair is a key strategic area for the company to meet the demands of extending the life of in-service components.
"In an unstable geopolitical situation, the supply chain faces major challenges in sourcing raw materials for the aerospace industry. This means that we need to extend the lifetime of in-service parts, which will in turn reduce the need for raw materials to produce new goods, saving us significant costs and the depletion of natural resources,” says Ceena Joseph.
"The collaboration with JTH has been excellent"
Ceena Joseph believes that research in circular repair helps to improve GKN's expertise and visibility in RePair and will increase customer value.
“The collaboration with JTH has been excellent in this matter. The expertise, critical thinking, teamwork and knowledge sharing, as well as the delivery of results on time was remarkable. A large amount of work was carried out, analyzed and delivered during these projects, which has led to the development of the technologies”, says Ceena Joseph.
List of externally funded projects in the area of "Circularity by Repair"
- SMART (funded by Vinnova/NFFP8): developing novel techniques for testing small repairs of Titanium alloys; 2023-2024; (Project leader: GKN Aerospace Sweden; other partners: JTH, Dalarna University), 3.42 million SEK; led at JTH by Ehsan Ghassemali.
- FAME (funded by Vinnova/NFFP8): advanced testing and optimization of Titanium alloy repairs that are made by additive manufacturing techniques; 2024-2028; (Project leader: GKN Aerospace Sweden; other partners: JTH, Dalarna University), 13 million SEK; led at JTH by Ehsan Ghassemali.
- SCALABLE (funded by KK-Stiftelsen): developing novel testing techniques and evaluation of small repairs of Nickel-based alloys; 2025-2027; (Project leader: JTH; other partners: GKN Aerospace Sweden; Härdservice Norden), 4.48 million SEK; led at JTH by Alireza Nazarahari.
- ALCIRCUIT (funded by MISTRA): Developing recyclable Aluminium alloys that are suitable for repair of large cast components; 2025-2028; (Project leader: Chalmers University; other partners: JTH, Lund University), 6 million SEK; led at JTH by Ehsan Ghassemali.
- Professor Materials and Manufacturing - Casting
- School of Engineering
- ehsan.ghassemali@ju.se
- +46 36-10 1692